Best ERP system for small manufacturing businesses with low budget? Finding the right software can feel like searching for a needle in a haystack. But don’t worry, we’re here to help you navigate the world of enterprise resource planning (ERP) and find a solution that fits your needs and your budget. This guide will walk you through the essential features, affordable options, and crucial implementation steps to ensure a smooth transition and maximize your return on investment.
From open-source wonders to cloud-based champions, we’ll uncover the best ERP systems tailored for small manufacturers without breaking the bank.
This comprehensive guide will equip you with the knowledge to choose the perfect ERP system. We’ll delve into the specifics of selecting the right features, exploring cost-effective options, and addressing the challenges of implementation and long-term maintenance. Get ready to streamline your operations and boost your bottom line!
Defining Needs for Small Manufacturing Businesses: Best ERP System For Small Manufacturing Businesses With Low Budget
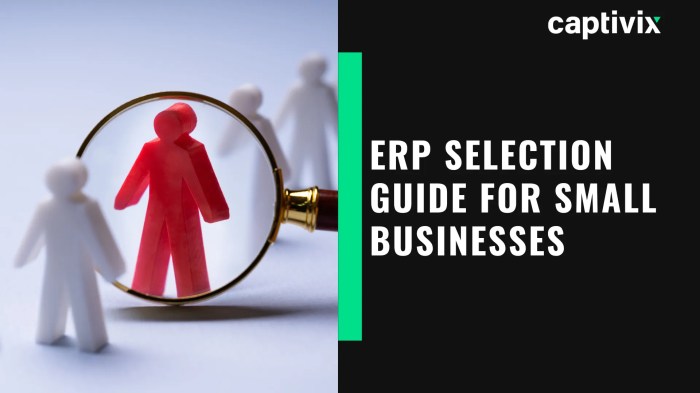
Choosing the right ERP system is crucial for small manufacturing businesses aiming for growth and efficiency. A well-integrated system streamlines operations, improves decision-making, and ultimately boosts profitability. Understanding your specific needs is the first step in finding the perfect low-budget solution.
Core Business Processes Requiring ERP Support
Small manufacturing businesses typically require ERP support across several key areas. These include inventory management, production planning, order fulfillment, customer relationship management (CRM), and financial management. Effective integration between these processes is vital for a smooth workflow. For example, accurate inventory tracking ensures that production doesn’t stall due to material shortages, while seamless order fulfillment improves customer satisfaction and reduces lead times.
A robust ERP system acts as the central nervous system, connecting these disparate functions and optimizing overall performance.
Essential Functionalities for Inventory, Production, and Order Fulfillment
In a low-budget environment, prioritizing essential functionalities is key. For inventory management, this means a system capable of tracking raw materials, work-in-progress (WIP), and finished goods, with accurate real-time visibility. Production planning needs to include features for scheduling, capacity planning, and materials requirement planning (MRP). This ensures that production runs smoothly and efficiently, minimizing waste and maximizing output.
For order fulfillment, the ERP should seamlessly integrate with inventory and production, enabling timely order processing, shipment tracking, and accurate invoicing. A simple, user-friendly interface is crucial for ease of use and adoption across the team.
You also will receive the benefits of visiting best offline horror games with jump scares and intense gameplay for PC today.
Reporting Requirements for Key Performance Indicators (KPIs)
Tracking key performance indicators (KPIs) is essential for monitoring business health and making data-driven decisions. Small manufacturing businesses need reporting capabilities that track production efficiency (e.g., units produced per hour), inventory turnover rate, on-time delivery, and customer order fulfillment time. The ERP system should allow for customized reports to be generated quickly and easily, providing insights into areas for improvement.
For instance, regularly analyzing inventory turnover can help identify slow-moving items and adjust production accordingly. Similarly, monitoring on-time delivery helps gauge customer satisfaction and identify potential bottlenecks in the supply chain.
Must-Have vs. Nice-to-Have ERP Features
Feature | Must-Have | Nice-to-Have |
---|---|---|
Inventory Management | Real-time tracking, low stock alerts, basic reporting | Advanced inventory optimization, barcode/RFID integration |
Production Planning | Scheduling, basic MRP, capacity planning | Advanced scheduling algorithms, shop floor control |
Order Fulfillment | Order processing, basic shipping integration, invoicing | Advanced shipping options, automated order tracking, customer portals |
Reporting | Key KPI reports (inventory turnover, production efficiency, on-time delivery), basic financial reports | Advanced analytics dashboards, custom report generation, predictive analytics |
Exploring Affordable ERP Options
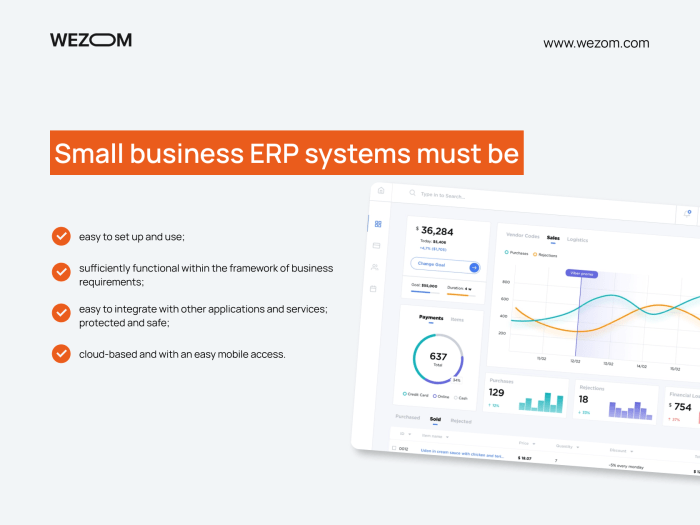
Finding the right ERP system for your small manufacturing business doesn’t require breaking the bank. Many affordable and effective solutions exist, catering specifically to the unique needs of smaller operations. This section explores some open-source and cloud-based options, comparing their pricing models and highlighting successful implementations.
Choosing the right ERP system is crucial for streamlining operations, improving efficiency, and ultimately boosting profitability. However, navigating the vast landscape of ERP software can be overwhelming, especially for businesses with limited budgets. This section aims to demystify the process by providing a clear comparison of several affordable options.
Open-Source and Cloud-Based ERP Systems for Small Manufacturers
Several open-source and cloud-based ERP systems offer cost-effective solutions for small manufacturing businesses. These options often come with lower upfront costs and flexible pricing models, making them attractive alternatives to expensive, on-premise systems. The key is to carefully assess your specific needs and choose a system that scales with your growth.
- Odoo: A highly versatile, open-source ERP system offering a wide range of modules, including manufacturing management, inventory control, and CRM. Its modularity allows businesses to select only the features they need, reducing costs.
- ERPNext: Another open-source option, ERPNext provides a comprehensive suite of tools tailored for various business types, including manufacturing. It’s known for its strong community support and active development.
- Tryton: A robust, open-source ERP system built on a modular architecture, offering flexibility and customization. While it has a steeper learning curve than some other options, its powerful features make it a viable choice for businesses with specific needs.
- SuiteCRM: While primarily a CRM, SuiteCRM’s open-source nature and extensibility allow integration with other manufacturing-specific tools, providing a cost-effective solution for managing customer relationships and related manufacturing processes.
ERP System Pricing Model Comparison
Understanding the different pricing models is critical for budgeting. The cost of an ERP system can vary significantly depending on the chosen vendor, features, and deployment method.
ERP System | Pricing Model | Typical Cost Range (USD/month or one-time) |
---|---|---|
Odoo | Subscription (per user, per module) | $20 – $1000+ (depending on the number of users and modules) |
ERPNext | Open-source (free software, paid support/hosting optional) | Free (software) / Variable (support and hosting) |
Tryton | Open-source (free software, paid support/hosting optional) | Free (software) / Variable (support and hosting) |
Note: Prices are estimates and can vary depending on specific needs and service providers.
Successful Implementations of Affordable ERP Systems
Several small manufacturing businesses have successfully implemented affordable ERP systems, resulting in increased efficiency and improved profitability. These examples highlight the potential benefits of choosing a cost-effective solution.
- A small furniture maker utilized Odoo’s inventory management and manufacturing modules to streamline production, reduce material waste, and improve order fulfillment. This resulted in a 15% increase in productivity within six months.
- A custom metal fabrication shop implemented ERPNext, leveraging its open-source nature and customization capabilities to create a tailored system that integrated with their existing machinery. This improved communication between departments and reduced errors by 10%.
Pros and Cons of Selected ERP Systems
Each ERP system offers a unique set of advantages and disadvantages. Carefully weighing these factors is essential for making an informed decision.
- Odoo:
- Pros: Highly modular, extensive functionality, large community support.
- Cons: Can be complex to implement, subscription costs can add up.
- ERPNext:
- Pros: Comprehensive features, strong community support, cost-effective.
- Cons: Steeper learning curve than some other options, customization may require technical expertise.
- Tryton:
- Pros: Highly customizable, robust and scalable.
- Cons: Steep learning curve, may require significant technical expertise for implementation and customization.
Evaluating System Features and Scalability
Choosing the right ERP system isn’t just about finding the cheapest option; it’s about finding a system that fits your current needs and can adapt as your small manufacturing business grows. This involves careful evaluation of several key factors beyond initial cost. A poorly chosen system can quickly become a bottleneck, hindering growth and efficiency.System integration with existing tools is crucial for streamlining workflows and avoiding data silos.
Scalability ensures the system can handle increased data volume and user demands without requiring costly upgrades or replacements. Finally, ease of use directly impacts productivity and employee satisfaction.
System Integration with Existing Business Tools
Seamless integration with existing software, such as accounting packages (QuickBooks, Xero), CRM systems, and e-commerce platforms, is paramount. Data duplication and manual data entry are significant time-wasters and potential sources of error. A well-integrated ERP system automatically shares data across different platforms, creating a single source of truth and improving overall accuracy. For instance, integrating your ERP with your accounting software allows for automatic transfer of financial data, eliminating manual reconciliation and reducing the risk of discrepancies.
This streamlined process saves valuable time and resources, allowing your team to focus on core business functions.
Scalability of the ERP System, Best ERP system for small manufacturing businesses with low budget
Scalability refers to the system’s ability to adapt to your business’s growth without requiring a complete overhaul. A scalable ERP system can handle increasing numbers of users, transactions, and data volume as your company expands. This avoids the costly and disruptive process of migrating to a new system down the line. Cloud-based ERP solutions often offer better scalability compared to on-premise systems, as they can easily adjust resources based on your needs.
For example, a small manufacturer might start with a basic cloud-based ERP package and easily upgrade to a more advanced plan as their production volume increases and their team expands, adding modules for advanced inventory management or supply chain optimization as required.
Ease of Use and User Interface Design
An intuitive user interface (UI) is critical for ensuring efficient adoption and maximizing user productivity. A user-friendly system minimizes training time and reduces the likelihood of errors. Look for systems with clear navigation, customizable dashboards, and helpful reporting tools. Poor UI design can lead to frustration, decreased productivity, and ultimately, a reluctance to use the system effectively. Compare different systems’ UI designs by exploring their demo versions or requesting online presentations.
Consider factors such as the layout, ease of data entry, and the availability of training materials. A well-designed system will feel intuitive and easy to navigate, even for users with limited technical expertise.
ERP System Comparison
ERP System | Key Features | Pricing (Approximate) | Scalability |
---|---|---|---|
Odoo | Inventory management, CRM, accounting, manufacturing modules, customizable | Varies greatly depending on modules and users; can start at low cost | Highly scalable; modular design allows for adding features as needed |
Zoho CRM + Zoho Inventory | Inventory management, CRM, sales order management, reporting | Relatively affordable; tiered pricing based on features and users | Good scalability; cloud-based solution allows for easy upgrades |
Acumatica Cloud ERP | Comprehensive ERP features including manufacturing, distribution, financials | Higher initial cost, but often offers better scalability for larger businesses | Highly scalable; suitable for growth, but initial investment is significant |
NetSuite | Full suite of ERP capabilities; strong in manufacturing and distribution | High cost, suitable for larger companies with more complex needs | Highly scalable, but significant upfront investment is required |
Implementation and Training Considerations
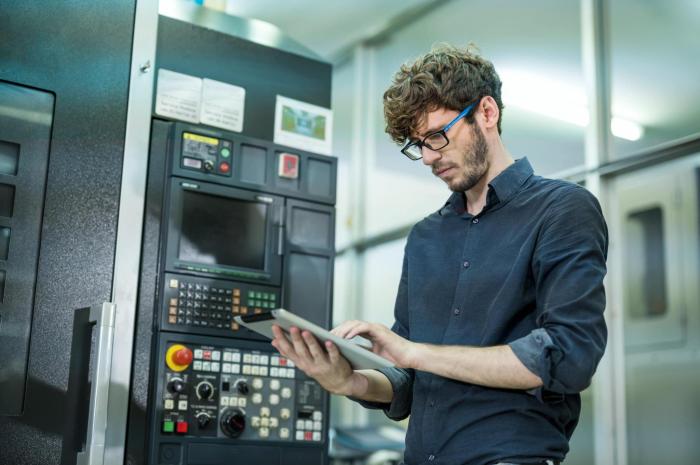
Successfully implementing an affordable ERP system requires careful planning and execution. A smooth transition minimizes disruption to your small manufacturing business’s operations and ensures a quick return on investment. This involves a well-defined implementation process, comprehensive employee training, and strategies to mitigate potential challenges.The typical implementation process for an affordable ERP system in a small manufacturing business often follows a phased approach.
This allows for incremental improvements and minimizes the risk of overwhelming your team. Ignoring this phased approach can lead to delays and frustrations, impacting productivity and morale.
ERP System Implementation Process
A phased approach ensures a smoother transition. For example, a small manufacturer might start by implementing the inventory management module, followed by production planning, and finally, integrating customer relationship management (CRM) functionalities. This allows the team to adjust to the new system gradually, rather than being bombarded with changes all at once. Each phase involves data migration, testing, and user acceptance testing (UAT) before moving to the next.
Thorough testing at each stage is crucial for identifying and resolving issues early on.
Employee Training Requirements
Effective training is paramount for successful ERP adoption. This is not a one-time event but rather an ongoing process. Initial training should cover the core functionalities relevant to each employee’s role. This might include data entry, report generation, and specific module usage. Follow-up training sessions and readily available support materials, such as user manuals and online tutorials, are crucial for reinforcing learning and addressing ongoing questions.
Consider incorporating hands-on training and real-world scenarios to enhance comprehension and retention. For instance, simulating production runs within the ERP system helps employees understand its practical applications.
Minimizing Disruption During Implementation
Implementing a new ERP system inevitably causes some disruption. However, strategic planning can significantly minimize this. Clearly defined roles and responsibilities, along with a dedicated project team, are essential. Regular communication updates to all employees keep everyone informed about the progress and address concerns proactively. Prioritizing data migration and system testing can also prevent unforeseen issues during the go-live phase.
For example, a phased rollout, starting with a pilot group before full-scale deployment, can identify and resolve problems before affecting the entire organization. This allows for adjustments and refinement of the process based on real-world feedback.
Step-by-Step Guide for a Smooth Transition
A structured approach is vital for a smooth transition. This involves several key steps.
- Project Planning & Team Formation: Establish clear goals, timelines, and responsibilities. Assemble a dedicated implementation team.
- Data Migration: Carefully plan and execute data migration from existing systems. Clean and validate data to ensure accuracy.
- System Configuration & Customization: Configure the ERP system to meet the specific needs of the business.
- Testing & User Acceptance Testing (UAT): Thoroughly test all system functionalities and gather feedback from users.
- Training & Support: Provide comprehensive training to all employees and establish ongoing support channels.
- Go-Live & Post-Implementation Support: Implement the system in phases and provide ongoing support to address any issues.
Following these steps ensures a smoother transition and minimizes disruption to daily operations. A well-planned implementation minimizes downtime and allows for a faster return on investment.
Long-Term Support and Maintenance
Choosing the right ERP system is only half the battle for a small manufacturing business. The ongoing support and maintenance are crucial for ensuring the system remains effective, efficient, and aligned with your evolving needs. Neglecting this aspect can lead to costly downtime, data loss, and ultimately, hinder your business growth. Investing in a robust support plan from the outset is a strategic move that protects your investment and safeguards your operations.Understanding the long-term costs and commitment involved with your ERP system is paramount.
This isn’t just about the initial purchase price; it’s about the ongoing investment required to keep the system running smoothly and updated with the latest security patches and features. Different vendors offer varied support packages, and understanding these differences is key to making an informed decision that fits your budget and operational requirements.
Support Options Offered by ERP Vendors
ERP vendors typically offer a range of support options, from basic email support to comprehensive, on-site service agreements. Basic packages often include access to online knowledge bases, FAQs, and community forums. Mid-tier options might include phone support during business hours, while premium packages often provide 24/7 phone and email support, along with on-site visits for critical issues. Some vendors also offer proactive maintenance services, regularly checking system health and performing preventative updates.
For example, a vendor might offer a basic plan for $500 per year covering email support, a mid-tier plan for $1500 per year including phone support, and a premium plan for $5000 per year with 24/7 support and on-site visits. The specific offerings and pricing will vary considerably depending on the vendor and the complexity of your ERP system.
Potential Costs Associated with Long-Term Maintenance and Upgrades
The cost of long-term maintenance and upgrades can be significant, and it’s essential to factor this into your budget planning. These costs can include annual maintenance fees, software updates, hardware upgrades, and the cost of technical support. Annual maintenance fees typically range from 15% to 25% of the initial software cost, depending on the vendor and the level of support required.
Major software upgrades, which might occur every few years, can add substantial costs, ranging from several hundred to several thousand dollars, depending on the scale of the upgrade. Additionally, unforeseen issues can arise, requiring additional support and potentially increasing costs. For instance, a sudden hardware failure might necessitate an unexpected expenditure on repairs or replacements. Proper budgeting and contingency planning are therefore crucial.
Checklist for Evaluating Long-Term Support
Before committing to an ERP system, it’s vital to thoroughly evaluate the long-term support offered by the vendor. The following checklist can help you assess the suitability of their support offerings:
- Service Level Agreement (SLA): Review the SLA carefully, paying attention to response times for different levels of support (e.g., critical vs. non-critical issues).
- Support Channels: Determine the available support channels (phone, email, online chat, etc.) and their availability (business hours only, 24/7).
- Technical Expertise: Inquire about the vendor’s technical expertise and experience with your specific industry and ERP system.
- Maintenance Costs: Obtain a detailed breakdown of the annual maintenance fees and any anticipated costs for future upgrades.
- Upgrade Process: Understand the vendor’s upgrade process, including the frequency of upgrades, downtime associated with upgrades, and the cost of upgrade support.
- Knowledge Base and Documentation: Assess the comprehensiveness and usability of the vendor’s online knowledge base and documentation.
- Community Support: Explore whether the vendor offers a user community forum or other support channels for peer-to-peer assistance.
Illustrative Examples of ERP System Use Cases
Let’s delve into practical scenarios showcasing how an affordable ERP system can revolutionize a small manufacturing business. We’ll focus on inventory management, production tracking, and reporting capabilities, using a hypothetical example to illustrate the points. Imagine “Artisan Crafts,” a small company producing custom-made wooden furniture.
Inventory Management for Custom Products
Artisan Crafts uses an ERP system to meticulously track its inventory. The system maintains a detailed record of each type of wood, its quantity, and its location within the workshop. When a customer orders a custom table, the system automatically checks if sufficient materials are available. If not, it generates alerts to the purchasing department, triggering a timely reorder.
This prevents production delays and minimizes material waste. The system also tracks the status of each component, from raw materials to finished goods, allowing for precise inventory control.
The ERP system’s real-time inventory tracking ensures Artisan Crafts always has the necessary materials on hand, while simultaneously preventing overstocking and reducing storage costs.
Production Progress Tracking and Bottleneck Identification
The ERP system at Artisan Crafts monitors each stage of the furniture production process. From cutting and shaping the wood to assembling and finishing, each step is meticulously recorded. This allows Artisan Crafts to track the progress of each order in real-time, providing valuable insights into production efficiency. If a particular stage consistently experiences delays, the system highlights it as a potential bottleneck.
For instance, if the finishing process consistently lags, Artisan Crafts can identify and address the issue, perhaps by investing in additional equipment or training.
By visualizing production flow and identifying bottlenecks, Artisan Crafts can optimize its manufacturing process, reduce lead times, and ultimately increase profitability.
Sales, Cost, and Profitability Reporting
The ERP system empowers Artisan Crafts with comprehensive reporting capabilities. It automatically generates reports on sales figures, breaking down revenue by product, customer, and sales channel. It also calculates the cost of goods sold (COGS) for each product, taking into account material costs, labor, and overhead. By combining sales data and COGS, the system automatically generates detailed profitability reports, allowing Artisan Crafts to identify its most and least profitable products.
This data-driven approach enables informed decision-making regarding pricing, production planning, and resource allocation.
The ERP system’s reporting functionality provides Artisan Crafts with a clear and comprehensive picture of its financial performance, enabling data-driven decisions for sustained growth and profitability.